Could you tell us any interesting facts or remarkable features about your project?
We celebrated our wedding in the garden here 28 years ago as my parents had lived here since 1989. When Andrew and I bought the original house from the family we had hoped to renovate it but its condition proved beyond repair. So, we did a salvage dismantle - a ‘soft strip’ first, retaining everything from cast iron baths to coat hooks then we used a salvage company to dismantle the house separating out bricks, timbers, tiles, metalwork etc. We rebuilt on the same footprint using an ICF material. Andrew and I cleaned 9,500 of the old bricks and scorched 1400 linear meters of our own larch with which we clad the new house. With the skill, diligence and creativity of our architectural technologist and builders we built a beautiful new home incorporating the best of new and old.
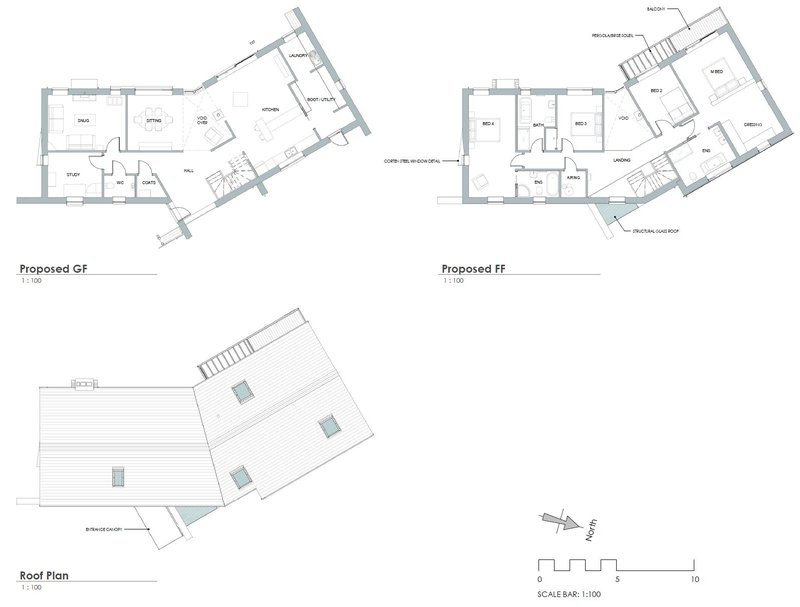
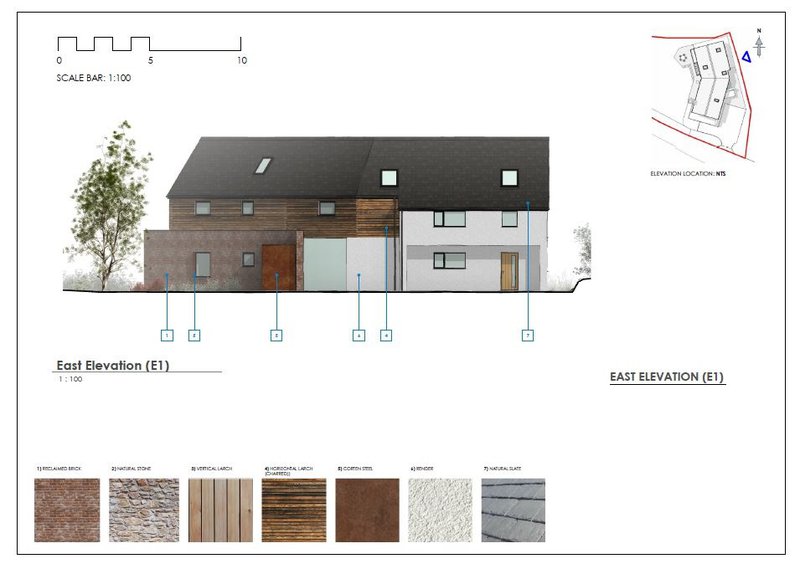
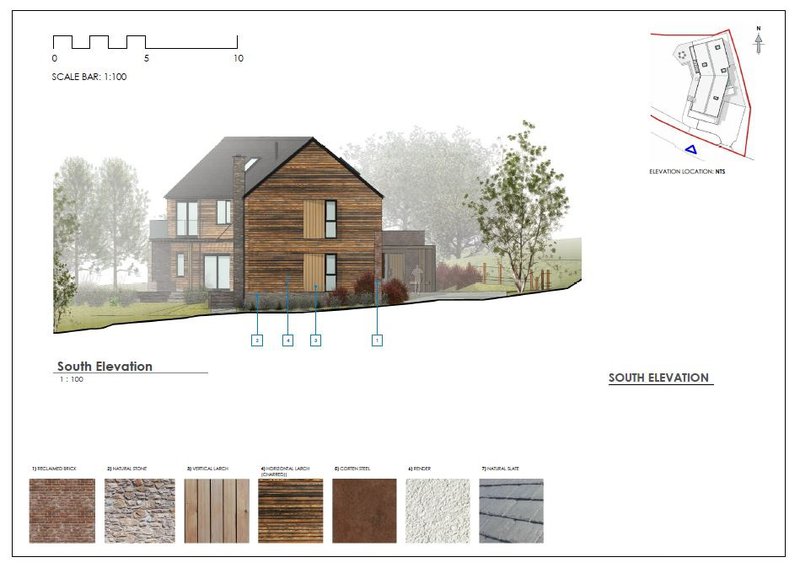
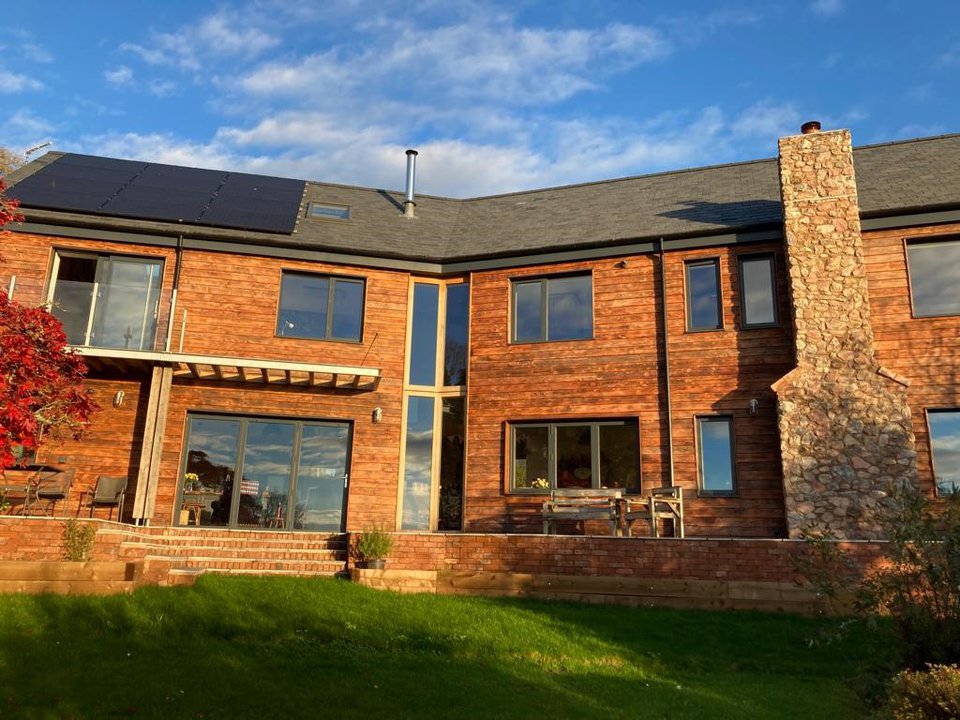
Sophie & Andrew's Experience at the National Self Build & Renovation Centre
How many times have you visited The National Self Build and Renovation Centre before?
We visited the NSBRC 4 times, including doing a Project Management Course there.
What would you say is the most helpful feature or resource at the NSBRC?
It was useful to see the wide range of exhibits and have certain processes explained and demonstrated in layman’s terms.
Did you use any exhibitors at the NSBRC? If so, who?
Durisol, NuHeat and Herschel Infrared.
What did you enjoy most about your visit to the NSBRC?
Enjoyed seeing such variety and becoming better informed. Staff and exhibitors were friendly and happy to answer even the most novice of questions.
Would you recommend the NSBRC to a friend, and if so, what aspects of the Centre would you recommend and why?
We’ve recommended NSBRC to lots of people! Particularly for the range of products; face to face with experts and demos; useful training courses.
‘The success of this project has been largely due to the aspect of collaboration and we would like to give credit to Vaughn Allington at 16a Architecture Ltd and Gareth Walker of CW Build Ltd, both of whom we would highly recommend.’
Information compiled in March 2022.