Lea & Peter Fellows - Case Study
What is the floor area of your project in sq ft or sq m?
330 sq m - excluding the garage.
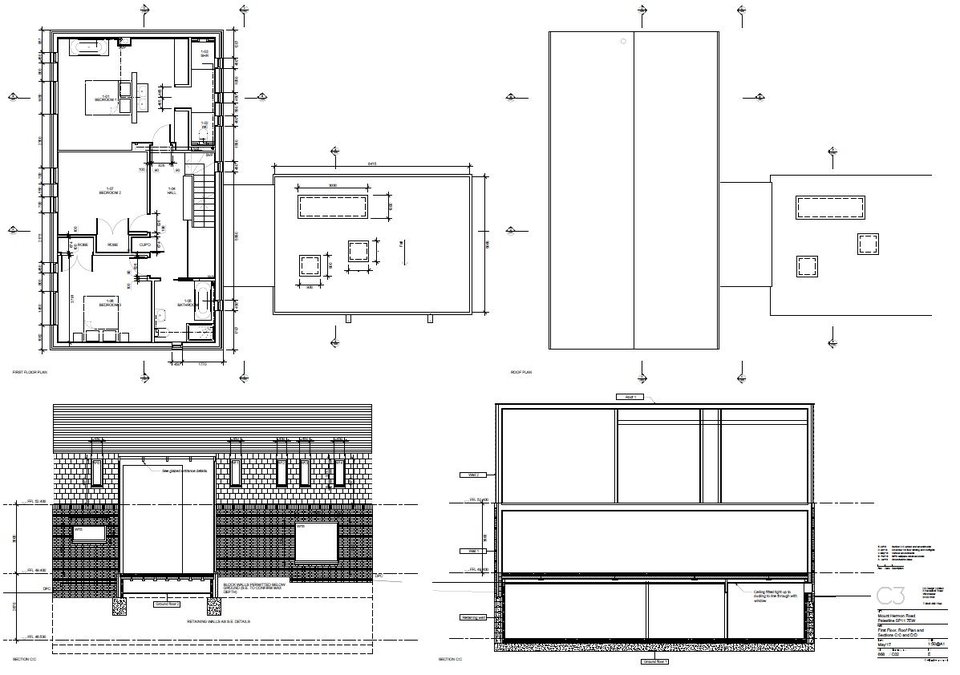
Could you tell us any interesting facts or remarkable features about your project?
The plot is not a particularly large plot but we were hampered by a village wide blanket TPO. So whilst we had 4 trees inside our border we actually had 15 TPOs along our boundaries (14 of which were Sycamores) which made construction for the builders a bit of a challenge. It also meant our Architect, Robin Haddow, who came up with the modern design, had to design around root areas which dictated the shape of the house and some build methods. The local planning department were generally supportive of what we were doing but trees seem to get them a bit excited.
We also particularly like how we have managed to get so much light in to the house at all times of the day. The double height glass link that encapsulates the entrance and hallway gives us light, shadows, stars and the sound of rain. It was a big expense but well worth it!
Finally, the technology has worked! Living with UFH, ventilation and an ASHP has been very different. You are literally building a micro climate which adjusts itself and provides a consistent environment. Everything can be controlled from your mobile phone which is a bit too far for some people but really does work.
Lea & Peter's Experience at the Centre
How many times have you visited The National Self Build and Renovation Centre before?
Circa 10 -12 times. We attended an Eco Workshop which guided our decision to include MVHR and ASHP. We have visited exhibitions which are always well attended by suppliers and experts. Plus we have just dropped in to reference a particular supplier, choose a brick or grab a magazine and browse. It really is a very good resource for self builders and has certainly shaped our project.
What would you say is the most helpful feature or resource at the NSBRC?
We self built 20 years ago and have been amazed by the changes to building systems, legislation and the possibilities available to self builders. All the information you need is here and if not they are able to connect you to the source. The people associated with the Centre are very approachable and hugely knowledgeable on their subjects. Every visit we made, we took away valuable information and answers to questions, even if it was to eliminate an idea or reinforce a particular route we were taking. Many of our major supplier and build system choices were either resident at the Centre or exhibited at one of the shows.
Did you use any exhibitors at the NSBRC? If so, who?
- Windows - supplied by Velfac
- Niko Home Automation - supplied by Swindon Home Control
- RK Door Systems - supplied by Freelance Entry Solutions
- Michelmersh bricks
- Nibe MVHR and ASHP - supplied by Sunstone Energy
- Ultraline sliding and bifold doors - supplied by Sightline
- Kingspan SIPS - supplied by Glosford SIPS
What did you enjoy most about your visit to the NSBRC?
The access times – the ability to call in to the Centre and have access to the reference material and publications as well as the wide range of courses run by the Centre and suppliers. The exhibitions too were always well run, informative and well supported by suppliers.
Would you recommend the NSBRC to a friend, and if so, what aspects of the Centre would you recommend and why?
Yes, we would highly recommend. We took advantage of almost everything the Centre has to offer. For us as self-builders, we took away something from the Centre every time we made a visit. We attended multiple national shows to widen our exposure to different suppliers & manufacturers.
It’s also a good reference for first timers. For us as second time self builders it was invaluable in updating our knowledge in the important areas of building regs, managing a budget and generally in the art of the possible.